In the modern world, the need for rare earth magnets is many times greater than we think. Not to mention there are products around us that need a magnet to work without us knowing it, sure when you know it, you will be surprised! Let’s learn about magnets, applications, and how to make them easy or not ^^
I. What is a magnet?
It is an object that can attract metals and their alloys. Magnets have two poles North and South. Around the magnet, there is always a magnetic field with magnetic field lines going from north to south.
II. Types of magnets
Alnico magnet: is a type of permanent magnet consisting of aluminum (Al), Nickel (Ni), and Cobalt (Co) components. Before the invention of rare earth magnets, Alnico magnets were the strongest magnets.
Ferrite magnet: it has the main composition of iron 3 Oxide (Fe2O3) and Barium Oxide (BaO). Ferrite magnets are cheap because the manufacturing process is not too complicated. Therefore, it is widely used for general applications, which do not require too high of a feature.
Samarium-Cobalt magnet: it is classified as one of the rare earth magnets. It is made up of two metal compounds, Samarium(Sm) and Cobalt(Co). This is the second most powerful magnet after Neodymium magnets. However, it has extremely good heat resistance and can be up to 500 degrees Celsius.
Neodymium rare earth magnet, symbol NdFeb, is a type of permanent magnet with the strongest magnetic force in the world to date. It is made from an alloy of Neodymium, pure iron, and Boron (Bo) forming Nd2Fe14B, referred to as NdFeB. Compared with other types of magnets, Neodymium magnets, despite having a smaller mass and size, have a much higher magnetic force. This is the type of magnet that is changing the world today.
III. Applications of magnets
- Computer, smartphone
We may be using computers, smartphones, smartwatches… In our daily lives, we have never questioned the presence of magnets inside it. However, magnets are one of the most important and indispensable ingredients in those products.
- Hybrid cars
The motor, one of the main components of a hybrid car, used for electromagnetic transmission, is equipped with a permanent magnet rotor and it rotates synchronously with a 3-phase AC frequency. Hybrid vehicles require lighter engines with more power. The permanent magnets used for them are neodymium-sintered. Because they have strong magnetic force with compact bodies. Neodymium-sintered magnets are expected to grow in markets where such motors with compact bodies and high performance are required.
- TV, audio speakers, radio
Magnets are used inside TVs, audio speakers, and radios. Small coils and magnets inside the speaker convert electronic signals into sound vibrations.
- Generator
Magnets are used inside generators to convert mechanical energy into electrical energy. In contrast, other types of motors use magnets to convert electrical energy into mechanical energy.
- Metal suction
Charged magnets can help cranes move large pieces of metal.
Magnets are used in refiners that separate metal ore from crushed rock.
It is also used in food processing industries to separate small metal flakes from grains etc.
Magnets can help collect all the nails scattered on the ground after repair.
At home, you use magnets when you stick a piece of paper on the refrigerator to remember something. Attaching a magnetic bottle opener to the refrigerator can be very helpful.
- Machines in the medical field such as MRI machines
Magnets used in MRI machines are used to create images of bone structures, organs, and tissues. Even magnets are used to cure cancer.
- Compass
We often use a pocket compass to find directions when going backpacking. The pocket compass uses a magnetic needle to point north.
- Bank card
The dark strip on the back of debit and credit cards is magnetic and is used to store data much like a computer’s hard drive.
IV. The production process of rare earth magnets with the presence of a series of equipment manufactured by ULVAC:
- Prepare raw materials (Nd, Fe, Boron, Dy, …)
The manufacturing process begins with the extraction of the raw materials needed to produce rare earth magnets.
- Scaling
In this step, we will weigh and measure different types of materials in appropriate proportions to make the molten mixture in the next stage.
- Melting/ Forming into long thin slices (Melting/ Casting)
Raw materials, which have been weighed in the appropriate proportions, are melted in a vacuum using a vacuum melting furnace. The alloy is melted in a mold. It is then poured onto a water-cooled rotating shaft. Alloys that are cooled suddenly will harden into thin pieces.
ULVAC’s melting methods are selected by magnet manufacturers:
Spindle melting and cooling – most common (FMI series)
In arc style (FMA series)
Plasma (FMP series)
Electron Shot (FME series)
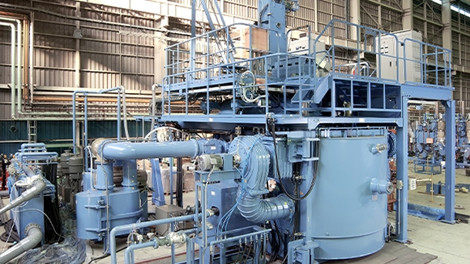
- Hydrogen decay
The products of the above process will be put into the hydrogen decomposition furnace chamber. Here the hydrogen gas is charged. The hydrogen atoms enter the interstitial position between the main phase of the compound and enter the boundary of the Nd ‘rich particles’, forming the interstitial compound. As a result, the distance between the atoms increases. The network volume is expanded. As a result, internal stress will produce crystal cracking. This process is accompanied by creaking sounds, so it is called hydrogen decay. This process is also known as the HD process. This decomposition provides a great advantage for the subsequent jet-crushing process.
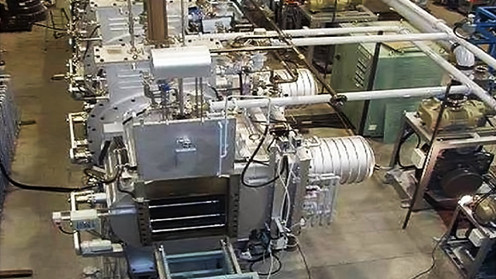
- Jet milling
This process uses a high-speed jet of inert gas. To accelerate the raw dough to supersonic speed and impact the dough against each other. The particle size after grinding determines the magnet’s performance. So this step is very important. After jet milling, the particle size reaches from 3 to 5 microns.
- Pressing
This is the process that uses the interaction between the magnetic powder and the external magnetic field. To align powder along the direction for easy magnetization. Magnetic-oriented pressing is the most common method for manufacturing anisotropic magnets. The Nd-Fe-B alloy was ground into a single-crystal grain in a previous jet milling process. The single-crystal particle is uniaxial anisotropy and each particle has only one easy magnetization direction.
- Vacuum Sintering (Sintering)
The particle density of the field-oriented pressing process is about more than 95% according to the theory. The sintering process helps to close the interwoven gaps in the grain network. To ensure uniformity of flux density and chemical stability. The sintering temperature of Neodymium Magnets is between 1,050 and 1,180 degrees Celsius. If the temperature is too high, it will lead to grain growth and reduce the internal coercive force. To obtain the ideal coercivity, after sintering the Neodymium magnets are annealed in two stages, 900 degrees Celsius and 500 degrees Celsius. This process is carried out in a multi-chamber continuous sintering furnace.
Please read the information about the ULVAC vacuum sintering furnace specialized for magnet production here.
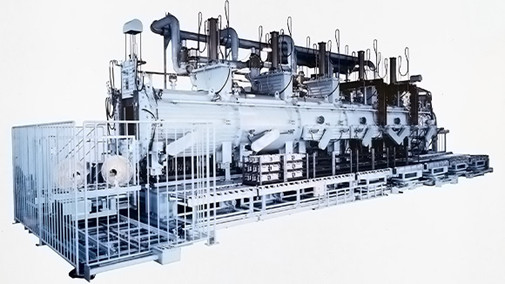
- Machining
In addition to the regular shape and moderate size, it is difficult for sintered Neodymium magnets to directly achieve the required shape and dimensional accuracy at the same time due to technical limitations in magnetic directional compression. field, therefore, machining is an inevitable process for sintered Neodymium magnets. Sintered neodymium is very hard and brittle so only cutting, drilling, and grinding technology can be applied to its machining process in conventional machining technology. Blade cutting usually uses diamond-coated or CBN-coated blades. The drilling process of sintered Neodymium magnet is mainly used diamond and laser.
- Magrise:
This process helps to increase the magnetic performance of the magnet, which is less susceptible to demagnetization in high-temperature environments.
A typical Dy-charged magnet has an elemental Dy content of 3%. But with the boundary diffused magnets with 3.5% Dy content by Magrise device, its magnetic performance will be better or equivalent to 7% content by conventional method => amount of Dy half off!
EPMA image showing Dysprosium spreading into the conformational boundary:
This Magrise device is patented by ULVAC, Inc.
- Aging
The aging process eliminates impurities, the magnet is as clean as possible, and there is no gas inside.
Vacuum aging furnace ULVAC
- Surface treatment
Surface protective treatment is a necessary process for Neodymium magnets. Sintered Neodymium magnets possess multiphase microstructure and consist of Nd2Fe14B primary phase, Nd-rich phase, and B-rich phase. The Nd-rich phase exhibits a very strong oxidation tendency and will form a primary battery with a primary phase in the medium. wet field. Small amounts of substituted elements have the potential to enhance the chemical stability of the magnet but at the expense of magnetic performance. Therefore, the protection of sintered Neodymium magnets is mainly aimed at its surface.
The surface treatment of sintered neodymium magnets can be classified into wet process and dry process. Wet process (QT) refers to magnets that are treated to a surface protection treatment in pure water or solution. Wet QT includes phosphate, electroplating, electroplating, electrophoresis, spray coating, and dip coating. A dry process refers to a magnet that has been treated to protect the surface through a physical or chemical process without contact with the solution. Dry processes typically include physical vapor deposition (PVD) and chemical vapor deposition (CVD).
- Magnetization
After being surface treated, the magnet needs to charge an external magnetic field. How to do it: place it inside a coil that, when an electric current flows through it, creates a magnetic field three times the strength needed by the magnet.
ULVAC prides itself on being a pioneer in the development of equipment to produce the most powerful magnets in the world.
In addition to providing equipment, we also support consulting overall solutions, maintenance, repair, and troubleshooting within 24 hours with a team of professional engineers from inside the South to the North. Hotline 24/24: 0988 248 567 (Mr. Ngoc) or 0936 151138 ( Ms. Hao)